Ogni azienda ha la sua organizzazione e l’organigramma traccia ruoli, responsabilità e relazioni gerarchiche o funzionali.
Attraverso le cosiddette “ReCo”, cioè incontri brevi tra attori chiave di un reparto con l’obiettivo di gestire le deviazioni dal target, riusciamo a raggiungere una chiara e robusta comunicazione tra livelli gerarchici ed informazione a tutti i livelli sulle prestazioni aggiornate della propria area; il tutto in modo efficace ed efficiente.
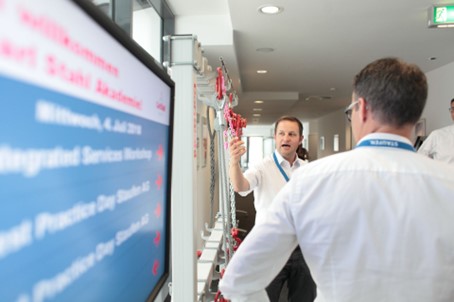
Una struttura organizzativa che è possibile incontrare, per esempio è quella detta a matrice.
La struttura a matrice è un mix tra organizzazione funzionale e organizzazione divisionale.
Si caratterizza, infatti, per la coesistenza di due linee di dipendenza: gerarchica (verticale) e funzionale (orizzontale). Questa particolare struttura organizzativa oltre ad essere caratterizzata da un’ampia flessibilità delle risorse presenta anche un’alta possibilità di conflitto tra i manager e i responsabili aziendali.
Ad esempio durante la progettazione di una ReCo, un responsabile potrebbe trovarsi nella condizione di dover prendere decisioni e assegnare dei task a dei riporti funzionali ma non gerarchici.
Come smarcare questa empasse, che spesso rappresenta solo un pro-forma politico?
La soluzione più ovvia sembrerebbe quella di modificare l’organigramma alla radice, ma qualora non fosse possibile ecco alcune soluzioni efficaci: coinvolgere sempre capo funzionale e gerarchico per trovare con loro un accordo sulle modalità di ingaggio nei confronti dei vari riporti; creare dei KPI “ad hoc” in modo da far convergere i due capi gerarchico e funzionale verso lo stesso obiettivo; definire criteri di escalation per la gestione a un livello superiore di queste dinamiche.
E voi, come affrontereste questa situazione?

